

Reise des Lichtreiters
Im Jahr 2015 haben wir ein ehrgeiziges Projekt in Angriff genommen. Ziel des Projekts war es, der Welt (und unseren potenziellen Kunden) zu zeigen, was mit Additive Manufacturing möglich ist, wenn es richtig mit unserem hochfesten Scalmalloy-Material und topologieoptimiertem Design kombiniert wird. Natürlich hatten wir bereits ähnliche Dinge hinter verschlossenen Türen unter Geheimhaltungsvereinbarung gemacht, aber diese Projekte waren streng geheim und durften nie das Licht der Welt erblicken. Wir hatten den brennenden Wunsch, den Leuten zu zeigen, wie cool das war, was wir machten, und das Light Rider-Projekt wurde zu einer Art Druckablassventil für das Team.
Viele Leute haben die spektakulären Videos und Bilder des Light Rider gesehen und viele Leute schreiben uns E-Mails mit der Bitte, eins zu kaufen. Wir meinen, dass es jetzt an der Zeit ist, zu zeigen, was wirklich nötig war, um dieses Fahrrad herzustellen, und warum es 2015 kein kommerziell tragfähiges Produkt war. Aber vielleicht auch, warum es das bald sein wird.
Dies ist die bisherige Geschichte der Reise des Light Rider …


Das Konzept
Das Light Rider-Konzept war ziemlich einfach. Wir wollten etwas schaffen, das die organischen Strukturen zeigt, die sich aus der Topologieoptimierung ergeben, und das zum Kernstück des Designs machen. Dies ist die Art von Struktur, die wir in allen möglichen Projekten geschaffen haben, aber selten in der Öffentlichkeit, und dieses Mal wollten wir, dass es jeder sieht.
Man könnte über die Zweckmäßigkeit eines offenen Rahmens streiten, über die Aerodynamik, darüber, ob er sauber ist … die Liste ist endlos. Aber über die optische Wirkung kann man nicht streiten. Ob man ihn mag oder nicht, man wird ihn bemerken, wenn er auf der Straße an einem vorbeifährt.
Wir wollten, dass Sie sich fragen, wer damit gefahren ist

Design
Eine Topologieoptimierung an einer einfachen Halterung durchzuführen ist heutzutage ziemlich unkompliziert, aber auf der Ebene einer Fahrzeugstruktur ist es eine ganz andere Herausforderung. Eine Vielzahl von Lastfällen muss berücksichtigt werden, und bei einer großen Struktur wie dem Light Rider müssen auch Gelenke und Kinematik berücksichtigt werden.
Als wir den Light Rider entwickelten, hatten wir nur eine EOS M290-Maschine mit einer Baukammer von 250 mm x 250 mm x 320 mm. Man muss kein Genie sein, um zu erkennen, dass der Rahmen nicht in einem Stück passt. Dies führt zu einem anspruchsvollen iterativen Designprozess. Wie teilt man ihn am effizientesten auf, wobei man die Einschränkungen von AM, Schweißen und die strukturelle Effizienz des Designs berücksichtigt?
Die Antwort lautet: mit Schwierigkeiten. Wenn Sie keine Leute haben, die diese Kompromisse schnell umsetzen können, werden Sie Probleme haben. Zum Glück hatten wir diese Leute, und das ist es, was uns bis heute auszeichnet.
Design für die Fertigung
Bei der Optimierung des Designs für die Fertigung gab es viel zu bedenken, insbesondere angesichts der geringen Größe der Baukammer, die uns damals zur Verfügung stand. Die verfügbaren Optionen bei der Aufteilung des Rahmens führten zu vielen möglichen unterschiedlichen Fertigungsergebnissen, und wir mussten in jedem Fall die Machbarkeit sowohl für AM als auch für das Schweißen berücksichtigen.
Die Entscheidung, wo das Design aufgeteilt werden sollte, hatte Auswirkungen auf die für den Druck erforderliche Ausrichtung und die Stützstrukturen und damit auf die Verschachtelungseffizienz und Produktivität des AM-Prozesses. All diese Entscheidungen hatten enorme Auswirkungen auf die Produktionskosten. Wenn das Design einfach von einem Maschinenbauingenieur definiert und an einen AM-Dienstleister weitergegeben worden wäre, wären die Ergebnisse möglicherweise nicht ganz das gewesen, was sie waren.
Bei APWORKS haben wir den Vorteil, dass beide Disziplinen im selben Team und in den meisten Fällen auch im selben Gehirn vertreten sind. Das hilft.
Trotzdem brauchten wir am Ende 12 Bauschritte, um alle benötigten Elemente herzustellen, und die kleine Baukammer führte zu einigen Kompromissen hinsichtlich der Ausrichtung der Teile. Das Ergebnis war eine lange Bauzeit und viel mehr Support als wünschenswert, aber es war nicht unmöglich

Herstellung
Die 12 Bausätze verliefen reibungslos, bis auf einen, bei dem es eine etwas peinliche (aber größtenteils amüsante) Situation gab, bei der zwei Teile so effektiv ineinander verschachtelt waren, dass sie nicht getrennt werden konnten. Ein bisschen wie die Ringe des Zauberers waren sie nicht wirklich verbunden, aber unmöglich zu entwirren. Solche Dinge passieren, wenn man an die Grenzen geht!
Die ganze Realität von AM ist in der Nachbearbeitung vollständig sichtbar. Viele Stützstrukturen müssen entfernt werden, viel Schleifen und Schmirgeln. Viel Handarbeit.
Die Auswahl der verwendeten Werkzeuge lässt darauf schließen, um welche Art von Arbeit es sich handelt. Weit entfernt vom versprochenen Traum des Star Trek-Replikators!
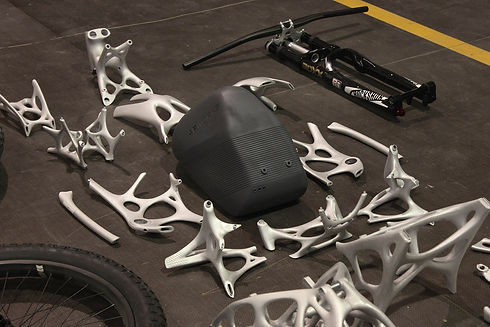
Das Kit
Neben der Vielzahl gedruckter Scalmalloy-Teile mussten wir auch die Batterieverkleidung aus selektiv lasergesintertem (SLS) Nylon herstellen. Alle anderen Komponenten wie Motor, Drehzahlregler, Batterien, Räder usw. wurden kommerziell bezogen und das Design wurde darauf abgestimmt.
Weniger als drei Monate nach Beginn des ersten Baus waren alle Teile des Prototyps zur Montage bereit. Mit einer einzigen EOS M290 bedeutete dies eine nahezu kontinuierliche Produktion während dieser Zeit. Es ist vielleicht schon leicht zu erkennen, warum das Produkt im Jahr 2015 als kommerzielles Unterfangen nicht wirklich rentabel war. Seitdem hat sich viel geändert, aber dazu später mehr.
Als nächstes mussten wir den Rahmen schweißen.

Schweißen
Trotz der vielen Schweißnähte in engen Räumen verlief das Schweißen überraschend gut. Vielleicht nicht ganz so überraschend, dank unseres hochqualifizierten Schweißers vor Ort, der alle Anerkennung dafür verdient.
Mit drei Armen ist es leichter...
Aber im Ernst, das Ganze fing an, wirklich schön auszusehen, und jetzt mussten wir nur noch alles zusammenbauen ...
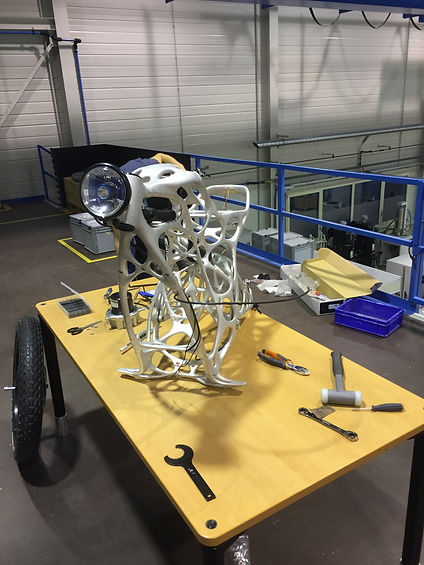
Montage
Wir haben dieses Bild nur eingefügt, weil es so aussieht, als würde man dieses süße Pixar-Lampen-Ding mit einer Robbe paaren ...
Wie auch immer, was soll ich sagen. Es war viel Herumprobieren damit, die Teile, die wir gekauft hatten, zusammenzusetzen und zum Laufen zu bringen. Nicht gerade Plug-and-Play, aber nichts, was wir nicht hinbekommen hätten. Alles in einem Tag Arbeit.
Oh, und so ziemlich jeder saß darauf und tat so, als würde er darauf reiten

Die Stunde der Wahrheit
Und dann endlich, weniger als 6 Monate nach Projektbeginn... geschah dies
Und der Rest ist Geschichte.
Aber jetzt müssen wir das noch einmal überdenken.
Ein großartiges Stück Marketing, ja.
Aber kein lebensfähiges Produkt, zumindest nicht im Jahr 2015.
Aber was ist heute?

Wie geht es weiter?
Seit 2015 hat sich in der Welt der additiven Fertigung viel verändert. Größere Baukammern ermöglichen eine viel effizientere Ausrichtung und Verschachtelung größerer Teile. Die Rohstoffkosten sind deutlich gesunken und natürlich sind die Maschinen produktiver geworden. All dies hat den Light Rider von einem unpraktischen Marketingobjekt zu einem fast praktischen Produkt gemacht.
Wird die Produktion billig sein? Nein, leider sind wir noch weit davon entfernt, diese Dinge in großem Maßstab und zu den Kosten produzieren zu können, die für den Verbraucher erschwinglich sind. Aber als Luxusprodukt ist es endlich im richtigen Bereich, um ein tragfähiges Angebot zu sein.
Deshalb sollten Sie hier im Auge behalten, um zu sehen, was als Nächstes kommt …