
The Highest Strength Aluminium Alloy for Additive Manufacturing
Scalmalloy
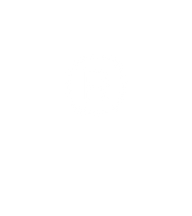

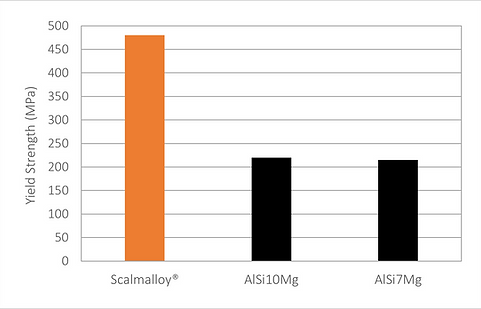
STRENGTH
Scalmalloy is the highest strength AM processable aluminium alloy, and is the only AM processable alloy which can effectively substitute high strength 7000 series aluminium alloys from plate or forging. Thanks to the low density of Scalmalloy it provides density-specific properties which are extremely competitive even with the highest strength alternatives.
Combining high strength with excellent ductility and processability, it is the ideal material for use in highly loaded and safety critical parts, which is why it is already applied in many critical applications.
​
Scalmalloy already has a proven track record in a wide range of applications in Aerospace, Robotics, Marine and Motorsport, and is an approved material under the the FIA regulations.
​
What is the real value of this?
With Additive Manufacturing the process time to build a part is the single biggest cost driver. Reducing the volume of the part by exploiting the higher strength of Scalmalloy therefore provides cost savings as well as weight savings, enabling you to win on both fronts.
CORROSION RESISTANCE
High strength usually means adding alloying elements which are detrimental to corrosion behaviour, which is why most high strength Aluminium alloys are susceptible to corrosion.
​
In the case of Scalmalloy we have utilised a strengthening mechanism which enables us to retain the excellent corrosion resistance of 5000 series alloys, as proven through numerous corrosion tests. We can also apply anodising or coatings to further improve corrosion behaviour.
​
Scalmalloy components have been used in diverse environments ranging from the cold vacuum of space, to the salt sprayed deck of racing yachts, to the heat soaked environment of racing car drivetrains.


DESIGN FREEDOM
With Scalmalloy you can have both the material properties of a forging combined with the geometric freedom of Additive Manufacturing, which surpasses that of casting.
​
We can weld Scalmalloy parts to make larger assemblies, overcoming the size limitations of AM, while retaining the design freedom and material properties which Scalmalloy provides.
​
Our most exciting projects are confidential, but we hope that the images we are able to share gives you a hint of what is possible, and inspires you to go further with your ambitions.
​
CONFIDENCE
Thanks to extensive testing over more than 10 years Scalmalloy is now one of the best understood materials for Additive Manufacturing.
It is a common misconception that taking any well known alloy composition and processing it using Additive Manufacturing (AM) is a short-cut to certification... it isn't
​
All the evidence of performance 'as-processed' by AM is still required, regardless of the chemistry of the alloy.
With Scalmalloy you can benefit from our experience and our extensive dataset.
Find out more about becoming a Certified Scalmalloy Partner
​
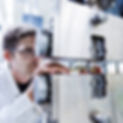